PT. Smelting has implemented Occupational Safety and Health according to ISO 45001:2018 in the integrated management system.
As the first copper smelter and refinery in Indonesia, PT. Smelting has a major role in creating a safe working environment through the process improvement which is efficient, sound and environmentally friendly as a model for future copper smelter.
PT. Smelting has the basic responsibility to assure OSH for all of its employees and subcontractors. In this information era, this issue has become dominant and vital for company continuous existence. PT. Smelting makes safety the highest priority for all workers and visitors.
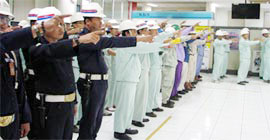
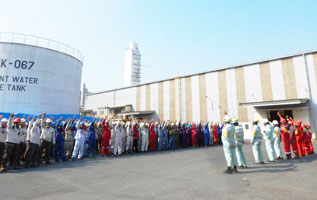
OSH Section has issued a general safety standard that must be followed by all employees, contractors and visitors. OSH Management System (OSHMS) consists of the entire safety standard prevailing in this company.
This system combines the safety and government rules into one safety manual which is maintained and updated regularly to cope with the latest condition. Safety audit, as one of management tool, is done regularly to check and monitor the system conformity throughout the activities.
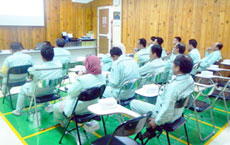
Safety Guidance Principles
All workers and visitors should get safety induction consisting of basic safety rules, hazards in the plant and emergency procedure they may face in PT Smelting. OSH Section treats safety as a main business value integrated in all activities. Principally, every accident causing injury or illness can be prevented from occurring by good planning of method, manpower, material selection and complete procedure.
Main Roles and Responsibilities
Managerial level bears the responsibility for the safety and wellbeing of workers and visitors working in his/ her area. Manager should proactively play a role in OSHMS application in his/ her working area.
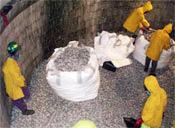
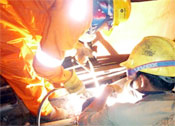
OSH Section has procedures in place for high risk jobs such as:
- Working at height
- Hot work (welding, lancing, gas cutting or grinding)
- Working in confined space
- Hazardous chemical handling
- Restricted area entry
- Digging work
Hazard Identification and Risk Control
Manager should confirm all risks in his/ her area have been identified, controlled and socialized to all employees. Personal protective equipment (PPE) should be identified, properly selected and provided according to the risk assessment. All employees and visitors should wear the provided PPE properly in order to stay safe and healthy during their entire service or stay in the plant.
Job Safety Analysis (JSA)
Job Safety Analysis (JSA) is compiled based on the results of the HIRARC analysis. Each activity requires JSA to ensure that the activity is done safely. JSA should be socialized to all workers.
Audit and Safety Patrol
To check the implementation of OSHMS in workplace, audit and patrol are done regularly. This activity can provide a feedback to the system improvement. The result of this activity is reported, and corrective action of the finding is then followed and implemented. Safety patrol is done by skilled and experienced safety officer and managerial staff to improve OSHMS implementation. Internal and external audit are done to maintain appropriate implementation of the system. External audit is carried out by competent and certified auditor from Manpower Ministry certified agency.
Near miss, Incident and Accident Analysis
Any near miss, incident and accident occurred are undesired event due to its loss to employees or production. This event should be investigated thoroughly and systematically by related parties by using the root cause analysis and then proper countermeasure for recurrence prevention should be established. Investigation report should be described in detail and completed with the clear time frame for the measure to be taken and its responsible person. OSH Section monitors the progress and makes sure all countermeasures are conducted timely, also make sure JSA review and revision is taken based on the result of investigation and countermeasure.
Emergency Response Program
Every section has Emergency Response Procedure (ERP) in place. This procedure has been socialized to all employees and workers in each section. This procedure should be drilled regularly with varying degree of risk by related sections to maintain section’s preparedness level.
Safety Training
Manager should continuously train his subordinates to improve their skill so they can implement OSHMS in their workplace. OSHMS implementation in workplace is mandated by government regulation therefore competent personnel in OSHMS implementation are very important element for the success.
To be competent in OSHMS implementation, an employee should cover these basic training requirements:
- Safety behavior
- OSHMS implementation
- Risk identification and control
- Safe procedure and methods
- Equipment and working tool
- Acquiring specific license
- Audit and investigation
Communication
Communication is an important factor in OSHMS. Every OSHMS program should be well socialized and communicated. Response and feedback from workers and visitors should be appreciated, addressed and used for system improvement.