What is 5 S ?
5S was developed in Japan and stands for the Japanese words Seiri (Ordeliness), Seiton (Tidiness), Seiso (Cleaning-up), Seiketsu (Standardization), and Shitsuke (Discipline). These words have been adopted to maintain "5S."
5 S is one of the methods of determining an organization approach to to evaluate its workplace organization capability & visual management standards. 5S engages people through the use of 'Standards' and ‘Discipline'. It is not just about housekeeping, but concentrating on maintaining the standards & discipline to manage the organization - all achieved by upholding & showing respect for the workplace every day.
5S consist of :
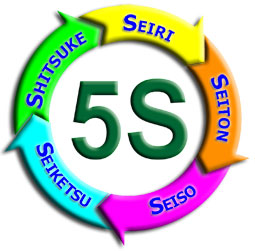

Seiri (Orderliness)

Seiton (Tidiness)

Seiso (Cleaning-up)

Seiketsu (Standardization)

Shitsuke (Discipline)
5S in PT. SMELTING
PT. SMELTING has applied and develops 5S movement since the company was born. The 5S movement in PT. SMELTING is activities focussing on good organizing of working area and build employee discipline habit to follow the procedure correctly. By the good condition of working place, the defect equipment and other problem can be detected earlier and prevented. And by the high level discipline of employee, the stable operation and good quality of production will be achieved and prevented from occupational accident.
All area in PT. Smelting divided in small area, we call segment. Totally PT. Smelting has 87 segments and decided one PIC for each segment. To keep spirit of 5S and in order to improved the 5S culture several activities was conducted in PT. Smelting which are:
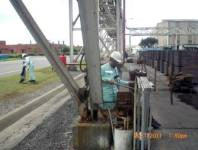
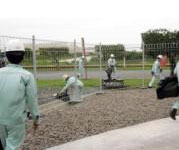
General Cleaning Activity
This activity was conducted by all PT. Smelting employee and sub-contractors every 2 weeks on Friday. In this activity, PT. Smelting employee and sub-contractor will clean up their working area start from 12.45 until 13.15 WIB.
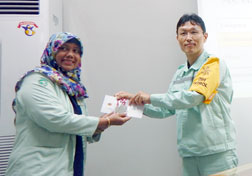
5S Monthly Evaluation Patrol
In order to evaluate and improved 5S movement in each segment, 5S Secretariat team will conduct patrol to all segments in PT. Smelting one time in a month. The result of evaluation including ‘Best Segment’, ‘Most Improved Segment’ and ‘Worst Segment’ will announced on Monthly Managerial Safety Meeting. General Manager will give award for the best segment and most improved segment.
5S Yearly Evaluation
5S yearly evaluation was conducted one time in a year at the end of year. The evaluator team consist of 5S internal auditor from 5S secretariat and each section representative (including sub-contractor). Result of yearly evaluation is categorized segment by 5 classes of 5S implementation, which are :
- GOLD : Area has excellent and develops 5S culture implementation.
- SILVER : Area has very good 5S culture implementation
- COPPER : Area has 5S culture implementation as standard.
- NO TITLE : 5S implementation still below standard, and
- NEED IMPROVEMENT : Area has no 5S culture implementation.
PT. Smelting will give reward for segment which achieved GOLD, SILVER and COPPER category.
East Java 5S Competition
Since 2003, PT. Smelting was invited and participated routinely in East Java 5S Competition for all categories (office, plant, environment, workshop and warehouse) which held by East Java Provincial Government. PT. Smelting has achieved several medals for that competition as show below :
5S Benchmarking and Training
In order to enhance knowledge of 5S implementation, PT. Smelting conduct 5S benchmarking to several companies in Indonesia which has excellent 5S implementation.
5S Evaluator and PIC of Segment area also given 5S training which provides by experience and competent consultant in order to improve 5S movement of working area and performance also quality of 5S evaluation activity.